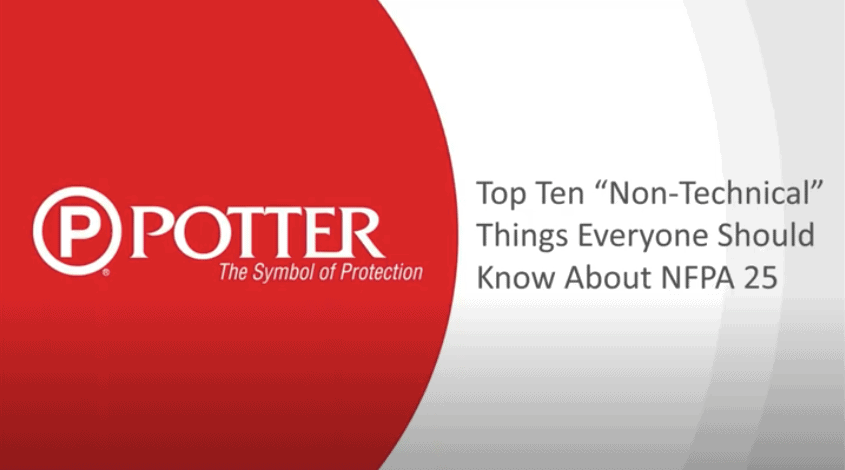
NFPA 25 exists to ensure the operational readiness of sprinkler systems if and when there’s a fire. It’s widely accepted that working sprinkler systems are the single best protection against unwanted fire. NFPA 25 serves as a standard to support sprinkler system success rates across industries and building types.
Problems with the sprinkler system mean lower chances of success in the case of a fire. And that means lives and property are at increased risk. NFPA 25 provides guidance on inspections and service of sprinkler systems to proactively catch issues and reduce the risk of missed problems. Ultimately, the goal is to ensure systems always work as intended.
Over time, the NFPA has revised and updated NFPA 25, with new editions released every three years. Different jurisdictions adopt new editions at different rates. The authority having jurisdiction (AHJ) sets the edition you have to comply with. Codes establish the “when” and “where” of ITM activities, while standards–like NFPA 25–establish the “how.” Essentially, NFPA 25 details ITM activities that are referenced by jurisdictional codes. Your AHJ’s code will reference a specific edition of NFPA 25–that’s the edition you have to stay compliant with.
Beyond the various editions, NFPA 25 can be a highly complex document–and not just on the technical side of things. Understanding how the document works, including how it defines certain terms, is essential for anyone with a stake in fire protection and fire sprinkler systems. We’ve compiled our top five non-technical things to know about NFPA 25 to help you stay compliant and better protect life and property.
1. ITM Requirements & Updates
NFPA 25 uses data to drive its guidance on the inspection, testing, and maintenance (ITM) of sprinkler systems. The NFPA releases an annual report, U.S. Experience with Sprinklers, that covers how well sprinkler systems have performed across industries and time.
The 2024 report identifies how often sprinkler systems operate effectively, the most common causes of failure, and the most common causes of ineffective operation:
Sprinkler Operations (2017-2021 Annual Averages)
- 89% operated effectively
- 8% failed to operate
- 3% operated ineffectively
Reasons for Sprinkler Failure (2017-2021 Annual Averages)
- 61% – system shut off
- 15% – manual intervention, defeated system
- 9% – system components damaged
- 9% – lack of maintenance
- 6% – inappropriate system type
Reasons for Sprinkler Ineffectiveness (2017-2021 Annual Averages)
- 48% – agent discharged did not reach fire
- 30% – not enough agent discharged
- 10% – inappropriate system for the type of fire
- 6% – system components damaged
- 4% – lack of maintenance
- 2% – manual intervention, defeated system
Source: NFPA U.S Experience with Sprinklers
Changes to NFPA 25 come, in part, from this data–the committee determines what areas need to be inspected and how frequently based on the most common causes of failure or ineffective sprinkler performance.
2. ITM Frequencies
It’s important to understand how NFPA 25 defines “frequency.” Frequency is simply defined as the minimum and maximum time between events. This means that, rather than true annual inspections (or any other inspection frequency), there are inspection windows. For example, specific inspections may need to take place between nine and 15 months apart.
The window allows inspections to remain compliant without taking place exactly one year (or any other amount of time) apart. In the example, as long as an inspection occurs in each calendar year more than nine months and less than 15 months after the last inspection, the building and system will remain compliant.
3. Responsibilities & Qualifications
NFPA 25 is very clear about who holds the responsibility for compliance with ITM standards: the building owner. This responsibility can be delegated to property managers, occupants, or another party with the correct documentation–but, ultimately, the owner bears the responsibility.
If the owner is responsible for compliance with NFPA 25, does that mean they are qualified to perform the necessary ITM tasks? Once again, we have to look at how NFPA 25 defines its terms. Someone who is “qualified” is competent, capable, and meets the requirements of the authority having jurisdiction (AHJ). For certain tasks, the building owner will be qualified. In fact, the standard expects that many required tasks will be performed by owners themselves.
As tasks become increasingly involved, the required qualifications become more extensive as well. The qualification needed for looking at a gauge is not the same as the qualification needed to perform an annual fire pump test.
One final note on qualifications: In NFPA 25, qualified does not necessarily mean licensed. Licensing requirements depend on the AHJ. While many states have licensing and certification requirements, some do not. Licensing requirements may be set at the local level as well. As long as the individual performing ITM tasks are competent, capable, and meet AHJ requirements, you remain compliant.
4. Record-Keeping
NFPA 25 requires building owners to create and maintain records for all ITM activities performed on their sprinkler systems. The requirements are basic and include records of who performed the inspection, test, or maintenance service; what service was performed; and when the service was performed. NFPA 25 also requires that the results of daily tests such as the pressure on the gauge or the temperature in the fire pump room be recorded. Historical records must be maintained to specific dates in order to be compliant.
5. Internal Assessments vs. Obstruction Investigations
The 2011 edition of NFPA 25 split internal inspection tasks into two sections: internal inspections and obstruction investigations. The 2014 edition renamed internal inspections to internal assessments, and shifted the prescriptive requirements of performing one. So, what’s the difference between internal assessments and obstruction investigations?
Internal assessments have a set frequency at which they must be performed: Every five years, to remain compliant, you have to open up the pipe and assess its internal condition. Internal assessments, by the definition outlined in NFPA 25, seek to identify foreign, organic, or inorganic materials within the pipe. Essentially, you’re looking for anything in the pipe that shouldn’t be there.
An obstruction investigation is not required at any frequency. Rather, investigations are performed on a needs basis–some systems may never need an obstruction investigation. The trigger for an investigation may be the identification of a problem during an internal assessment or another issue that indicates a problem on the inside of the pipe.
Watch the webinar for five more!
Introductions (03:06)
No 1. Why do fire codes require compliance with NFPA 25? (04:53)
No 2. Where does NFPA 25 come up with the ITM requirements? (08:06)
No 3. How are ITM frequencies established? (12:14)
No 4. Who is responsible for ITM and compliance with NFPA 25? (15:39)
No 5. Who can perform ITM? (16:45)
No 6. Which edition of NFPA 25 applies where I’m located? (21:05)
No 7. What records are required? (24:06)
No 8. What is the difference between an internal assessment and an obstruction investigation? (26:11)
No 9. What do internal assessments/inspections tell you? (29:50)
No 10. How do I change NFPA 25? (31:34)
Questions from the Audience (35:47)
Want support conducting NFPA 25-compliant inspections? See how Inspect Point can help.
Book a Demo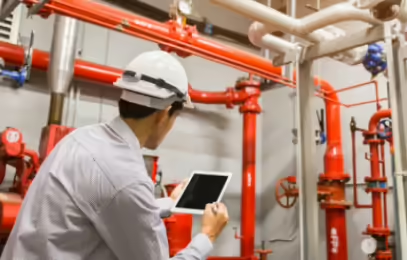